The main function of the car leaf spring guide seat is to limit the position, limit the lateral movement of the leaf spring, and ensure that the leaf spring and the frame are in the same plane, together with the car leaf spring to form a car suspension system to improve the comfort of the car. And stability. Usually, the relative movement between the leaf spring and the guide seat due to the change of the load of the car causes the leaf spring guide seat to wear more seriously, especially when the car turns or drives on the winding road, the lateral movement of the leaf spring is more frequent, thereby causing The wear of the side wall of the leaf spring guide seat is serious, or the leaf spring has a certain impact on the side wall of the guide seat due to the difference of the road conditions, resulting in serious wear or even breakage of the side wall. In this paper, the failure mode of the leaf spring guide seat is explored, and the failure reason of the leaf spring guide seat is explored, and corresponding measures are proposed to solve it.
Failure analysis
During the road test, a certain model of the company found that the working surface of the bottom or side of the guide seat was in contact with the leaf springs with different degrees of wear. Therefore, the failure parts were classified and classified: one type is the leaf spring guide seat. The bottom surface is seriously worn, and the other type is that the side and bottom surface of the leaf spring guide seat are seriously worn, and the side surface even has a fracture phenomenon.
It can be seen from the failure sample that the support base and the leaf spring support contact bottom surface and side surface have experienced severe wear. From the residual unworn surface, the amount of wear on the underside of the guide seat is 1 to 10 mm, and the support surface of the leaf spring guide seat with the most serious side wear has completely worn through until it breaks.
Material analysis
Sampling the failed parts and testing the chemical composition. The test results are shown in Table 1.
Table 1 Test results of chemical composition of failed parts


It can be seen from the analysis of the results in the table that the chemical composition of the material is not abnormal and meets the requirements of material grade QT500-7.
2. Mechanical properties test
The base of the failed component base and the side substrate were dissected and sampled for hardness test. The test results are shown in Table 2.
Table 2 Hardener leaf spring guide base hardness test results
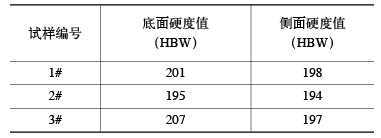
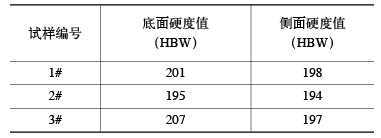
The hardness of the failure piece base is about 200HBW, and the mechanical properties are qualified, which meets the mechanical performance requirements of QT500-7 in GB/T1348-2009 "Spheroidal Iron Castings".
3. Metallographic microstructure analysis
The failure piece is sampled (the sampling part is the bottom surface of the guide base and its side) for metallographic microstructure inspection, and the test results are shown in Figures 1 to 4.
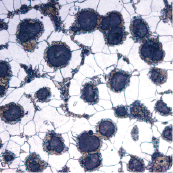
Figure 1 Metallographic microstructure of the substrate 400X
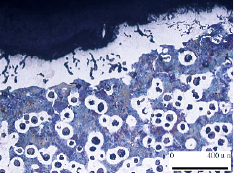
Figure 2 Local decarburization of matrix structure
The metallographic microstructure of the failed sample is graphite spheroidized grade 3, graphite size is 5-6, pearlite content is 45%-55%, metallographic structure is graphite+pearlite+ferrite; bottom and side metallographic analysis No abnormal structure was observed, and there was a decarburized layer in the surface layer of the sample. The depth of the decarburization layer was 0.15 to 0.2 mm, as shown in Fig. 4.
4. Discussion and results
Through the analysis of the material, mechanical properties and metallographic structure of the failure member guide seat, the performance of the leaf spring guide seat meets the relevant technical requirements of the national standard. The local presence of the decarburization layer on the failure piece may be the cause of the wear failure, but due to the decarburization layer. It is thinner and will not cause its wear resistance to be seriously reduced and will fail.
After analysis, the object that forms the "friction pair" with the bottom surface and the side surface of the leaf spring guide seat is the leaf spring suspension. After the steel plate spring is quenched and tempered, it has good plastic toughness, and the hardness is at least 40HRC (380HBW) or more. When the vehicle is heavily loaded on a road surface with complicated working conditions, the leaf spring is subjected to a certain load deformation and contacts with the guide seat to form a friction pair, so that the relatively low-hardness leaf spring guide seat wears poorly and wears until the fracture fails. When the hardness ratio H0 of the two members forming the friction pair is between 0.7 and 1.3, the friction performance is optimal. Therefore, it is recommended to heat-treat the leaf spring guide seat to increase its hardness to improve its wear resistance.
In view of the two types of failure modes of the leaf spring guide seat and the service conditions in the actual work, quenching and hardening the wear part is an effective way to solve the wear problem. This paper strengthens the surface layer by induction heat treatment. Has a certain wear resistance without changing the performance of the part matrix.
Process test
It can be seen from the above failure analysis that the bottom surface and the side surface of the leaf spring guide seat are the main failure parts. Therefore, in the process test, the induction heat treatment technology is used to simultaneously quench and strengthen the bottom surface and the side surface of the leaf spring guide seat to improve the strength and resistance. Grinding purpose.
1. Design of special sensor
In order to simultaneously induce heat treatment of the bottom surface and the side surface of the leaf spring guide seat, a special inductor is designed according to the size of the inner space of the leaf spring guide, the structural design and the corresponding quenching technical requirements, as shown in FIG.
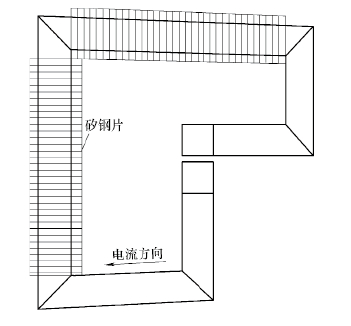
Figure 3 shows the effective heating part of the dedicated sensor
2. Induction quenching process parameters
The equipment used for induction heat treatment is a vertical universal quenching machine with a power supply of IGBT 300kW/50kHz. Induction quenching power 80?90kW, frequency 7kHz, continuous heating scanning quenching, during the heating process, the leaf spring guide seat is fixed on the special fixture and remains, the inductor moves in its inner cavity, the sensor moves speed 160mm/s, quenching agent For clear water, the quenching agent pressure is 0.1 MPa. Since the bottom surface of the leaf spring guide seat has a certain curvature, the gap between the inductor and the bottom surface of the leaf spring guide seat should be properly adjusted in the direction of the vertical inductor during the quenching process to ensure the consistency of the depth of the hardened layer of the part.
3. Process test results
The anatomical analysis of the quenched samples was carried out to determine the metallographic structure, the depth of the hardened layer and the hardness range in the quenched area. The quenching area can be judged macroscopically according to the heat quenching trace: the curved bottom surface is all hardened, and the side quenching height reaches 2/3 of the side height, as shown in FIG. 4 and FIG. 5.
The metallographic examination of the quenched sample was carried out, and the depth of the quenched layer was as shown in Figs. 6 and 7.
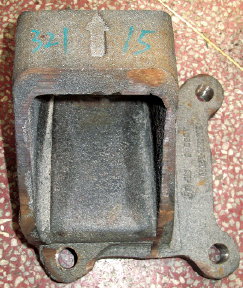
Figure 4 Sample quenching area
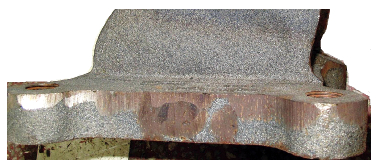
Figure 5: Side quenching and quenching of the sample
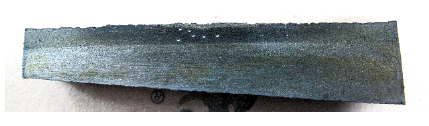
Figure 6 Sample hardened layer thickness on the side
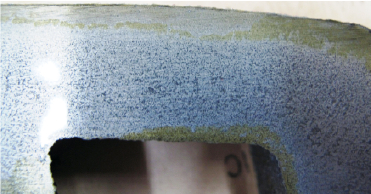
Figure 7 Thickness of hardened layer on the bottom of the sample
After testing and analysis, the surface hardness of the leaf spring guide seat is 50~54HRC, the hardened layer depth is 4.5mm (see Figure 6); the bottom surface (arc surface quenching layer distribution) surface hardness is 46~50HRC, and the hardened layer is 4~ 4.5mm (see Figure 7); the metallographic structure of the hardened layer is martensite and a small amount of undissolved ferrite, as shown in Figure 8.
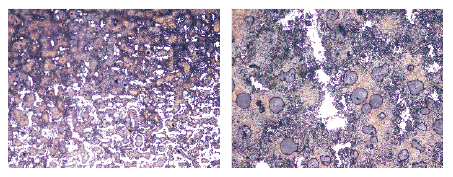
Figure 8 Metallographic microstructure of the sample hardened layer
4. Test
More than 8600 pieces of leaf spring guides strengthened by induction heat treatment are all loaded into the road test. There are no two failure modes similar to the ones in this paper, which completely solves the problem of bottom surface and side wear or wear fracture failure of the leaf spring guide seat. Provide technical support for future product development.
From the results of this process test and loading road test, it is possible to verify the feasibility of the induction heat treatment process on the bottom and side of the leaf spring guide seat. According to the characteristics of the induction heat treatment technology, the technical requirements for the induction heat treatment of the leaf spring guide seat are formulated:
1) The bottom surface of the leaf spring guide seat is completely quenched in the longitudinal direction, and the unhardened area of ​​the bottom edge of the bottom surface near the side is ≤10 mm.
2) The side quenching height of the leaf spring guide seat is greater than 2/3 of the cavity height.
3) The quenching hardness of the bottom surface and the side surface of the leaf spring guide seat is ≥45HRC.
4) The hardened layer depth of the bottom surface and the side surface of the leaf spring guide seat is 3-6 mm, and the hardened layer depth is inspected by the metallographic method.
Conclusion
The main failure mode of the leaf spring guide seat is that the bottom surface or the side surface or both sides are severely worn until fracture. The main reason is that the leaf spring guide seat has low hardness and poor wear resistance and wears up to wear and tear with respect to the leaf spring suspension. It is proposed to use the induction heat treatment technology to strengthen the leaf spring guide seat to improve its wear resistance; the bottom surface and the side surface of the leaf spring guide seat are developed simultaneously with the induction heat treatment process. The feasibility of the induction heat treatment process was verified by road test on the bottom and side of the leaf spring guide seat. The condition of induction heat treatment of leaf spring guide seat is established: the bottom surface of the leaf spring guide seat is completely quenched, the unhardened area of ​​the edge of the bottom surface close to the side is ≤10mm; the side quenching height is greater than 2/3 of the height of the leaf spring guide seat; the bottom surface The quenching hardness of the side and the side is ≥45HRC; the depth of the hardened layer is 3?6mm.
Mosquito Killer Lamp,T5 Bl Tube,T5 Bl Lamp,T5 Bl Bulb
Changxing leboom lighting product CO.Ltd. , https://www.leboomuvd.com