JUCENTER 6L: CBN high efficiency grinding machine
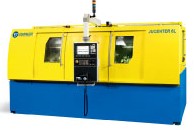
JUCENTER 6L processing example:
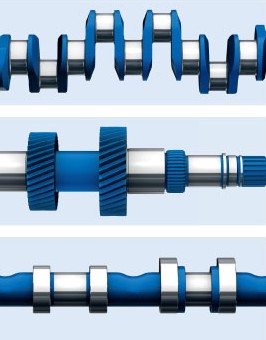
Professional advantages of the production line: overall grinding of the camshaft
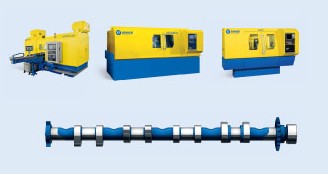
Grinding the shaft end. For the final production scenario, seven machines will be used, which will result in a tact time of only 20 seconds. This line solution is suitable for efficient mass production of camshafts. The use of a continuous CBN process ensures extremely high dimensional accuracy and surface quality with significantly reduced production cycles.
Grinding of wind turbine gearbox shaft
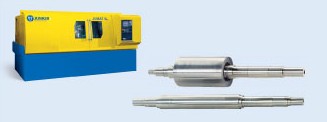
Data security guarantee through EJ-Backup

In addition to the daily backup backup, manual data protection can also be implemented through the call of the JUPRO operator interface. And a lot of data is also stored in that integrated flash card.
Door panel: door panel is made of stainless steel 304 with no frame. Core materials are paper honeycomb, aluminum honeycomb, PU, EPS and etc. The installation sites of door lock, door closer and hinge are reinforced with square tubes of more than1.5mmthickness which are compression moulded by special technology.
Door frame: it is made of completely stainless steel 304. The connection types with wallboards are double-clip type and aluminum connection. The former is applied mostly to machine made wallboard and the latter hand made wallboard. The accessories are double window and lift type sweeping bar. The lock can be famous door lock or the owners can select lock brands themselves.
Specification: common sizes 800X2100, 900X2100, 1500X2100 or1800X2100, can customize to customers` requirements, the materials can be selected according to customers` requirements such as306Lor other special materials.
Features: the stainless steel 304 door we produced are of elegant appearance, sturdy and durable, acid and rotting resistance and thermal insulation. It is the first choice for high-end projects at home and engineering concerning foreign affairs that requires for anticorrosion and high quality such as electronics factory and food factory
Hospital Sliding Door,Hospital Automatic Sliding Door,Hospital Sliding Glass Door,Hospital Sliding Ward Door
Shenzhen Hongfa Automatic Door Co., Ltd. , https://www.highspeedshutterdoor.com