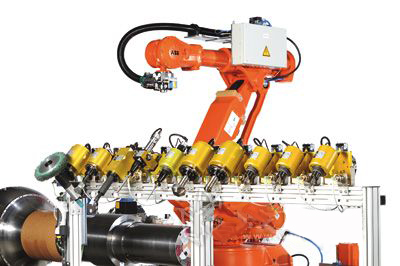
The robot unit can be driven on a single rail and machined a generator shaft with a deburring tool such as the DeburFlex 250 to a total length of 1 km.
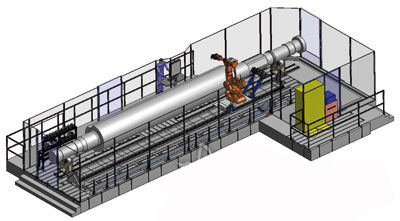
The machining program is set up and simulated offline on a 3D model of the unit and a generator shaft that needs to be machined.
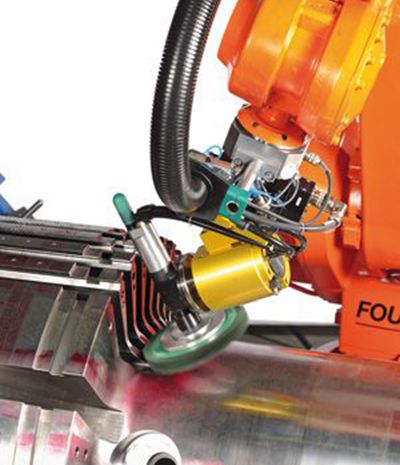
The West Deuterium DeburFlex 250 floating deburring spindle tool enables good results in deburring the generator shaft
Ultra Plantâ„¢ Grow Light offers One Chip Technology aimed to meet your indoor growing expectation such as improve plants' quality, increase yield, or better the margin, etc., all for helping you realize a higher return on your crops.
Ultra Plantâ„¢ Grow Light is combined our advanced All-In-One technology with patented optical design and customized light full spectrum supported from our experienced LED engineers, plant specialists and other partners working on horticulture.
From Ultra Plantâ„¢ APP, you are able to schedule the growing process including photoperiod, brightness and spectral in advance. The lighting system will help you grow smarter, easier and better.
Ultra Plantâ„¢ is the most versatile horticultural grow lighting fixture for indoor plants with flexible full spectrum, brightness control and uniform, wider light distribution, suitable for top lighting of all types of crops. No matter it applies to anywhere for any crop, Ultra Plantâ„¢ can do perfect work for you.
365Nm Led Grow Light,365Nm Led Grow Lights,Best 365Nm Led Grow Lights,365Nm Grow Lights
Feton Corporation , https://www.fetongrowlight.com