Business background
Suzhou Sufuma Machinery Co., Ltd. (hereinafter referred to as Sufula) is a leading enterprise in the wood-based panel industry. It is China's particleboard production line, medium (high) density fiberboard production line, double-sided thick sanding machine, sanding sawing line, short cycle. A professional manufacturer of wood-based panel equipment such as quick veneer production lines and horizontal immersion drying lines. The company is a national key enterprise, a key high-tech enterprise of the National Torch Program and a high-tech enterprise in Jiangsu Province. Sufuma has won 2 national-level scientific and technological progress awards, more than 10 provincial and provincial scientific and technological progress awards, more than 10 national key new products, and more than 10 patents have obtained national invention patents and utility model patents.
Background of the project
Sufuma's product types are mostly small-volume, customized products. After decades of development, the company has gradually formed a business management model that conforms to its own characteristics. The product data records the main management methods of each department by hand. As business needs continue to change, companies require the design, quality, production, and marketing departments to respond quickly to business needs. Sufuma has stepped up its informatization construction and applied CAD, CAPP and ERP. With the in-depth discovery of the application, the information data of the product design department has not been effectively managed and cannot be timely and accurately transmitted to other application departments. The Suffolk Manager decided to choose a flexible and scalable technology platform to build an information system that meets the needs of its own business processes. The system addresses the following issues:
Drawing document management
A large number of CAD electronic drawings and product data of the design department are scattered in the hands of designers due to lack of centralized management, and the security and confidentiality of data cannot be guaranteed. At the same time, due to different design habits, there is no uniform standard organization storage of product information, and multiple copies of the same file are prone to occur. Design documents are stored separately, so its storage, access, version management, access, change management, and consistency of electronic data and paper data are not scientifically managed, let alone associated with existing projects. It is.
Standardized purchased parts, standard parts libraries and codes
The Suffolk Design Department has no standardized management of purchased parts and standard parts. Each designer is named according to his own habits when selecting, resulting in the irregularity of material naming and the existence of “one object and multiple codesâ€. At the same time, the company's parts and components do not have a unified classification number standard, only the figure number, does not form an enterprise-level unified coding center, can not be used by subsequent systems.
Component and product structure management
The management of the company's products and parts is managed manually by the designer. The drawings and detailed design need to be modified by a special person and generate a BOM. It is impossible to quickly configure the BOM information.
Product and component process management
The existing approval process of the system is carried out manually on the drawings. It is very random, the manual name is easy to counterfeit, and sometimes there are signs of signing or missing.
Change management
Product design changes frequently, no change information is recorded, CAD drawings are not versioned, and the history of product quality and change cannot be effectively monitored and queried.
Collaborative management
The product data of the design, process, manufacturing, procurement and other departments of Suffolma have not been accurately and uniformly managed. There is a lack of correlation between CAD, CAPP, and ERP that is dominated by core business processes.
solution
The Suffolk manager finally chose the “PLM Product Lifecycle Management System†to establish a unified design and application platform for design and process, and was implemented by the technical team of Beijing Axter Technology Co., Ltd., supported by ExtechPLM core technology, and finally reached Shorten product design and manufacturing cycle, greatly improve the standardization degree, completeness and consistency of technical documents, improve the reuse of information resources, reduce the time for technical document retrieval, sending and receiving, and review, and finally lay a solid foundation for Suffolk to achieve digital manufacturing. The basics.
Establish a unified product development data management system
Relying on the PLM platform to establish a standard technical document management system, standardized management of product drawings, schedules and related electronic documents, providing accurate, consistent and complete product technical data for subsequent production, procurement, finance and other departments.
Create a BOM standard system
Tight integration with CAD, automatic creation of BOM structure in PLM, and rapid implementation of design changes through BOM replication to improve the efficiency of the R&D department. It appears in the system to manage the components of one or more products in a structured tree. It is convenient to build products and realize the reuse of common parts and borrowed parts of products.
Effectively manage product electronic documents and data
Unified management of product databases, management drawings, schedules, and related documents in PLM, providing accurate product technical data for production, procurement, and finance departments, and providing convenient tools for querying, browsing, borrowing, and exporting reports.
Component and product structure management
Establish a preferred mechanism for resources, and standardize the library of purchased and purchased parts of the company. Calling of related materials through the system. Realize the classification management of parts and components, realize the borrowing of product common parts, standard parts and outsourced purchased parts, and the deformation design, knowledge accumulation and reuse of products.
Technical management management system
Control design data input, review, release, output, and change management. Organize, manage and display product data information according to product structure (BOM), browse and query related drawings and technical documents on the nodes of each product and each part.
The designer manages his product data information in his personal workspace, receives assigned task information in a timely manner, performs assigned tasks, and submits task files. Monitor progress and quality at any time, and coordinate and change task attributes according to actual status to ensure that each task is completed on schedule.
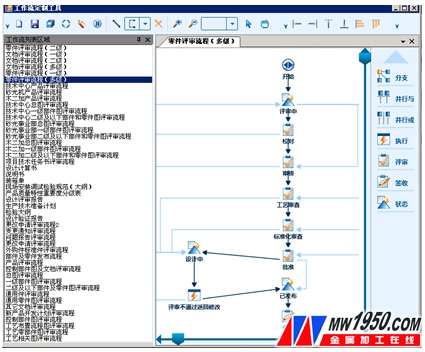
Standardize enterprise technology management processes and implement data file process control
Define and manage workflow templates to enable online review of real-time workflow process documents.
Effective management and control of design changes
Manage component changes, history, change message quick notifications and sign-off feedback, making it easy to query for changes.
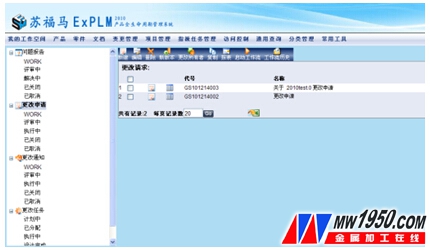
Enterprise knowledge management and accumulation
The PLM platform precipitates and effectively manages the accumulated experience, design plans, product materials, process knowledge and other resources in the process of enterprise development, laying a technical foundation for product innovation design.
system integration
Extech PLM has a flexible technology core that integrates existing tools and system data from CAD, EPLAN, CAPP, ERP, Office, etc. into the PLM application platform to help companies build a true product lifecycle management system.
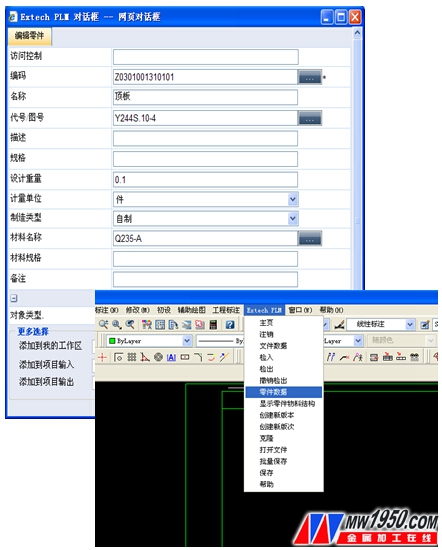
Operational status
The Suffolk PLM system has recorded more than 1,000 products, all of which are processed through PLM and CAPP, and purchased parts and standard parts can be quickly imported into CAD drawings. The material code automatically generated by the PLM system has become the company's unique identification code. PLM's process approvals are fully regulated. Various types of data can be easily and flexibly imported into subsequent information systems such as ERP.
Business income
Through the implementation of the ExtechPLM project, the level of information management of Suffolma has been greatly improved, and the potential information island problems of various departments have been effectively solved, and the electronic management of map documents, processes and technical data access has been realized. The new product design cycle and manufacturing cycle are shortened. The standardization, completeness and consistency of technical documents have been greatly improved. The recycling rate of information resources is more scientific and intelligent. Reduce the time for technical document retrieval, sending and receiving, and review. In the end, it laid a solid foundation for Suffolk to achieve digital manufacturing.
Testimonials during the implementation of the project
The implementation of informatization projects is a major reform of enterprise management, and implementation difficulties are more within the enterprise. Enterprises need to face the existing problems together with the software service providers. They must adhere to the requirements of the enterprise management process, adhere to the established solutions, ensure that all functions of the system are realized, and successfully complete the predetermined goals. In the specific operation, it is mainly based on the actual application, and the operation is simplified as much as possible from the perspective of the user, and the project is accelerated. After the project is successfully put into operation, it will increase promotion efforts, promote the wide application of various departments, and create high-value returns for enterprises.
Grow lights
Shenzhen Huangtai Photoelectric Co.,Ltd. , https://www.huangtailightstrip.com